The textile printing industry is evolving rapidly, driven by growing consumer demand for speed, customisation and sustainability. While screen printing has long been the backbone of high-volume garment production, it now faces increased pressure to keep up with a market that rewards agility and environmental responsibility. To stay relevant and profitable, screen printers need to rethink their production strategies – enhancing their capabilities rather than replacing what already works.
This is where a new hybrid approach makes all the difference, combining the strengths of screen with the agility of digital. With innovative direct-to-garment solutions like Kornit Apollo, the Industry’s mass-production powerhouse, businesses can handle short runs, personalisation and sustainability demands without compromising speed or quality. This isn’t just about keeping up – it’s about moving ahead.
The pressures facing today’s screen printers
Screen printers are navigating a perfect storm of operational and market challenges. Labour shortages and rising wages make it harder to staff and maintain efficient production lines, while outdated manual processes create bottlenecks that slow turnaround and inflate costs. At the same time, customers now expect on-demand delivery, personalised products, and short-run orders – preferences that traditional screen setups aren’t built to accommodate without wasting time and materials.
Environmental expectations add further pressure, as regulators and consumers alike call for cleaner, more responsible production. Water usage, chemical discharge and energy consumption have all come under scrutiny, putting traditional workflows at odds with sustainability goals. And with online platforms offering instant ordering and ultra-fast fulfilment, the competition is fierce. To stay ahead, screen printers must evolve, boosting efficiency, agility and sustainability without compromising quality or profitability.
Solving modern challenges through digital innovation
The answer isn’t to replace screen printing – it’s to enhance it with the right digital partner. Kornit Apollo was built to answer these very challenges, redefining what’s possible in a hybrid production environment. The one-step system, operated effortlessly by a single operator, leverages advanced automation capabilities to minimise the reliance on manual labour and eliminate traditional bottlenecks in production. It offers the agility needed to deliver one-offs or short runs just as efficiently as high volumes, all without the screen setups that make small orders inefficient in traditional workflows.
Sustainability is at the core of Apollo’s design, with a waterless process, eco-certified inks, and minimal waste and energy use. Aligned with global standards and consumer demand for greener production, it enables fast, high-quality output while empowering screen printers to expand into new markets and services – from on-demand drop shipping to personalised e-commerce – without disrupting existing operations.
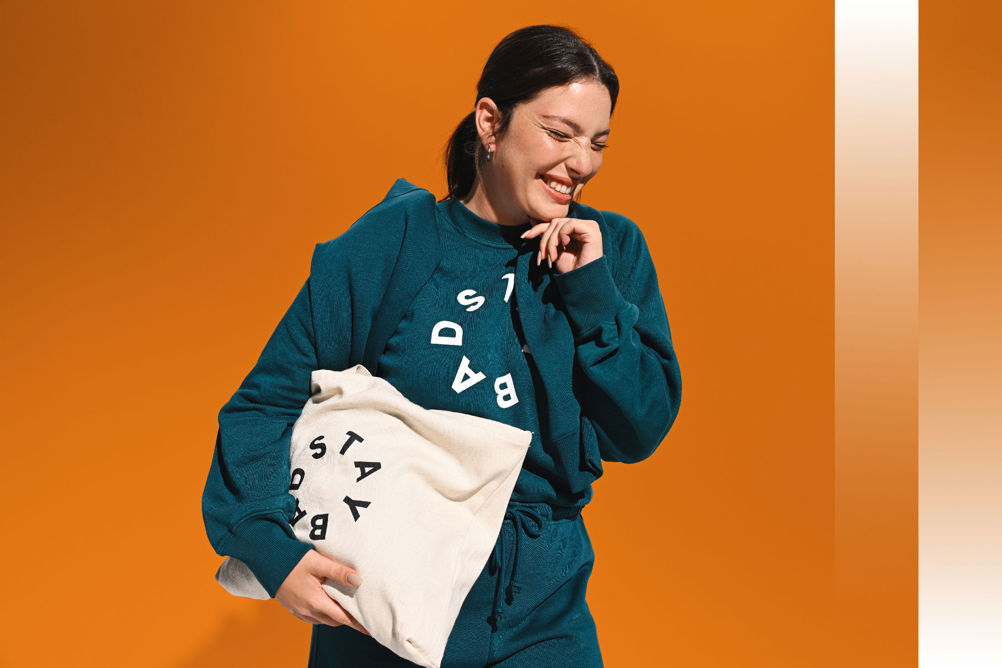
Your competitive edge with Apollo
What truly sets the Kornit Apollo apart is its ability to deliver retail-quality output, with exceptional spot colour accuracy and print consistency, alongside industrial-grade performance, digital flexibility and the mass-production efficiency required to excel in even the most demanding, time-sensitive projects. With unmatched speed, the Apollo can produce up to 400 garments per hour, meeting the most demanding production schedules with ease. Its semi-automated loading and automated unloading system streamlines operations, while auto-sized pallet shifting adapts seamlessly to different garment sizes for maximum efficiency. This level of reliability and automation ensures consistent, superior quality across every print, meeting the rigorous standards of licensed brands and high-expectation customers alike.
The business model behind Apollo is just as innovative: Kornit’s all-inclusive click pricing covers ink, maintenance, and support in one predictable pay-per-print rate. That means easier budgeting, and clearer profit margins, enabling printers to price confidently and scale with control.
Apollo’s integrated workflow streamlines the entire process – from order to finished product – cutting manual steps while boosting speed and accuracy. Backed by Kornit’s expertise and dedicated support, it’s more than a printer – it’s a scalable solution for limitless growth.
The future of print is hybrid – are you ready?
For screen printers looking to future-proof their operations and tap into new profitability, digital integration isn’t a trend, it’s a strategic imperative. The Kornit Apollo offers a seamless path forward, complementing traditional workflows while delivering speed, flexibility, broader offerings and sustainability at scale. It’s not about replacing what works, it’s about empowering it.
To experience this transformation firsthand, visit us at Fespa and see the Kornit Apollo in action. Discover how your business can evolve from screen to hybrid and lead the next chapter of textile printing.
To discover how Kornit technology has supported the evolutions of businesses like yours, click here.