For Surrey-based large-format specialist Fuel4 Print, conversations that began around two years ago, for a multitude of reasons, eventually led the team to face down that beast.
The challenge
“Staff were cramped, machinery was outdated and our processes were slower than they could be in this day and age,” explains Richard Gibbs, co-founder and managing partner of Fuel4 Print parent company, Fuel4.
Launched in 2006 as a bespoke design and build firm for exhibitions, fit outs and product launches in the travel and retail industries, Fuel4 originally outsourced its print work. However, in 2018, plagued by delays and unsatisfactory work, the business brought printing in-house with the creation of its own print division, Fuel4 Print.
The 15-strong print team surpassed all expectations and soon began servicing clients directly, building an enviable client list that today makes up two thirds of the division’s £1.2m turnover with the remaining third comprising Fuel4’s in-house work.
Located a stone’s throw from the Thames, in a leafy business park close to Staines town centre, Fuel4 Group already occupied units 4 and 6 on the site, housing the printroom and workshop and Fuel4’s office and warehouse respectively, but Fuel4 Print’s operation quickly outgrew the 750sqm space so a decision was made in 2021 that a move was essential.
With the decision made, the focus of the conversation then shifted to upgrading their print technology in an effort to further improve throughput and boost efficiency.
“Once we knew what we were going to upgrade to, we knew we’d be able to build out around that,” Gibbs says.
At the time, the division was running a flatbed printer with roll-to-roll option alongside two HP Latex 360s and a Latex 365. But Fuel4 Print managing director Mark Lyne explains he was keen to invest in a dedicated flatbed in the first instance, to speed up production, and a new roll-to-roll further down the line.
Eventually the team decided to invest in a Fujifilm flatbed, ordering the brand new Acuity Prime L 3.2x2m, the UK’s first, to be delivered in June this year, and plans for the new premises evolved from there, he explains.
The method
As part of their premises search, the team considered moving location rather than remaining in Staines, but as Gibbs points out, with unit 5 on their existing site becoming available and with complete redesign potential, staying put was a more attractive option.
“A big percentage of our work is airport work and a lot goes into Europe so we knew our location in Staines was good, being based near Heathrow,” he explains.
Gibbs adds: “We needed the print to stay next to us as it services the whole group and also we felt that moving away would be a big disruption for all of our staff. So although staying here was more expensive, when we weighed things up, particularly staff happiness, we decided to stay.”
A lease for the new unit was signed around nine months ago with the plan to move the whole Fuel4 Print operation into the neighbouring 750sqm building but completely refit it and build a 50x10m mezzanine, almost doubling its size. Unit 4 meanwhile, was kept to expand Print4’s wood and metal workshop.
Lyne, alongside his print team and with Fuji partner, Colyer, who advised on the purchase and installation of the Acuity, began to set out what the ideal environment would look like.
“We knew how much space we needed and the conditions we wanted for the new Fuji. So with a blank canvas we were able to build around it,” explains Lyne. He details how important it was to make sure the whole team had input. “It really was a collective thing,” he says.
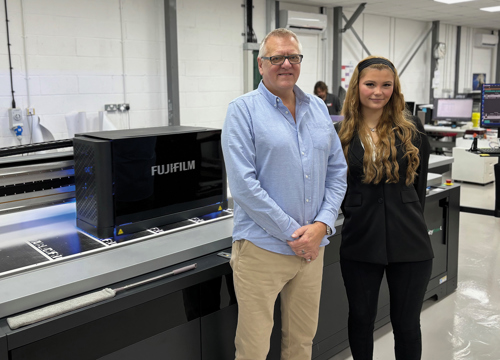
He continues: “We got the floor plans and diagrams, did CAD plans of the whole layout and included the existing and new equipment. Literally we had a scaled printout. We could see the spaces and what was available to us and we spent hours and hours putting things in and moving things around on the designs until we finally came up with a plan that we thought worked perfectly.”
The layout was based primarily on efficiency and making the production workflow slicker and in turn the staff’s jobs easier. The design and build process took three months from beginning to end and Lyne says that while it overran by around three weeks, due to a change of plan for the mezzanine stairs and late delivery of air conditioning units, that wasn’t a big issue.
“We also delayed a bit because the new machine didn’t come in on time and we didn’t want to move in until the new machine was in,” he says. “There were probably lots of things in the process that we could have done differently but we overcame everything anyway. We knew how everything was going to go in, the lights, furniture, power points, the kit. It was all finished and painted exactly as we wanted and ready for us to just move our things across the car park and move in.”
The result
Since Fuel4 moved into its new home at the end of June this year, the team has benefitted from a much improved working environment, better lighting, more efficient heating and air conditioning and much more space to get the job done, according to Lyne.
“There’s never a good time to outlay vast sums of money and of course it’s a bit nerve-racking when you’re doing it, but once we were in we were so glad we’d done it. It has massively benefitted us,” he states.
Lyne says that although the planning and decorating was, at times, “a headache” the result is a lovely working environment that is positively impacting both staff and visitors alike.
“Previously we were falling over one another and now we have things placed so the work flows through logically, painlessly and efficiently and allows more space in general for storage before and after printing.
“The height of the ceiling has made a huge difference and with daylight bulbs it’s brighter and more airy than before – it’s just created a nicer atmosphere,” Lyne remarks. Added to that productivity has “gone through the roof” since installing the Acuity Prime and he says the whole project has been a real success.
While the move centred around the installation of the new Fuji printer and improving workflow efficiency, the Fuel4 team also factored in room for growth in both staffing and equipment. The old SwissQprint has now been sold, with Lyne eyeing the fabric market and planning to take on a 3.2m roll-to-roll in mid 2024.
“Everyone seems to be going down the line of fabric light boxes and fabric window displays instead of the traditional print and cardboard, so we really want to start working with fabric. The lightboxes are easier to change and cheaper than digital lightboxes. We can print fabrics but we don’t have the silicone edging currently, so that is something we’ll bring on board at some point so we can print and finish fabrics,” he explains.
On the staffing side, Lyne explains that the business is changing shape slightly in that it is employing art workers so existing staff can focus more on the print and finishing side, while it will also recruit for sales, production and accounts staff.
“We are changing, adapting and evolving. We need to be. The future is bright,” he states.
Fuel4 Print, part of Fuel4 group
Inspection focus Speccing out a purpose-built site. How to plan, build and equip a new site to meet your specific requirements
Business location HQ in Staines, Surrey, plus an office in Florida, US
Inspection host Mark Lyne, Fuel4 Print managing director; Richard Gibbs, Fuel4 group co-founder and managing partner
Size Fuel4 Print staff: 15; turnover: £1.2m Fuel 4 Group staff: around 40; turnover: £5m
Established Fuel4 Print: 2018; Fuel4 Group 2006
Products and services Internal wall and floor graphics, external and wayfinding signage, glass signage, retail displays, exhibition and event graphics and retail displays
Kit Fujifilm Acuity Prime L, three HP Latex 365s, Kongsberg cutting table and two laminators
TOP TIPS
Because there are so many moving parts when it comes to a project like this, it’s important to be fairly flexible and not expect everything to go exactly according to plan but also know your boundaries, Lyne says. “Overall it overran by around three weeks. But that’s the way it goes and that sort of time is acceptable,” he states.
Lyne says it’s imperative to make sure you get other people involved in the planning. “I like to involve people in my thinking and decisions - you have to be willing to listen to the people that are using the equipment. They know it best,” he states.
Advance planning is key if you’re to hit the ground running, he explains, because so much can go wrong with a build that would have an impact further down the line. “Plan it well, draw it out, play about with it, think about the workflow. Don’t just rock into a place and say I want it to look like this and fill it up. A lot of thought and planning needs to go into it,” he advises.